- The Column
- Posts
- 馃彮 Veggie-based solutions
馃彮 Veggie-based solutions
Idemitsu is offsetting styrene transport, BASF's sustainable propylene glycol, and acrylonitrile.
TOGETHER WITH
Good afternoon. Today's edition is sending at noon CT, but since The Column's readership is global, I'm not sure how much the time of send matters鈥攍et me know:
Do you read The Column based on when it arrives? |
From the condenser:
路 Idemitsu is offsetting styrene transport
路 BASF's sustainable propylene glycol
路 MOTD: acrylonitrile
CARBON CREDITS
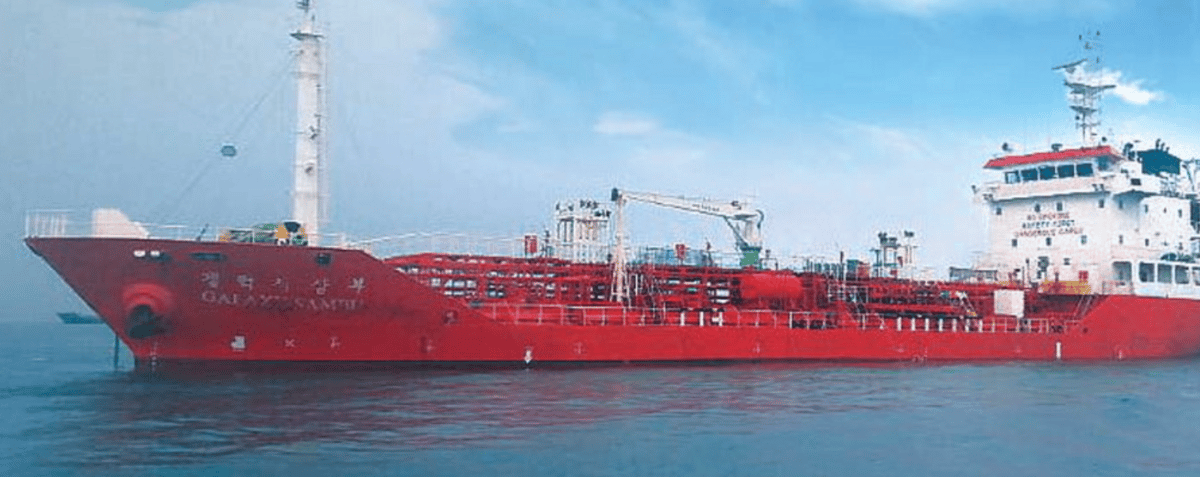
Idemitsu's carbon-offset styrene voyage
Japanese petroleum company, Idemitsu, offset the shipment of some bio-based styrene from Japan to Taiwan with carbon credits.
Wait, what are they shipping?
If you see a six-membered ring in some chemical or polymer, there's a good chance it can trace its roots back to the catalytic reforming of naphtha; a fraction distilled from crude oil. But we can make naphtha, or something really similar to petroleum-derived naphtha, via more sustainable means鈥攆or example, Valero's newest renewable refinery (which hydrotreats, isomerizes, and refines vegetable-based triglycerides) produces 10% naphtha. You could then use that bio-based naphtha to produce bio-based benzene (which later goes on to become styrene), toluene, and xylene.
Okay, so what's up with the carbon credits?
Carbon credit markets consist of two types of buyers: a) those who need to buy carbon credits because they emitted more than what their government said they were allowed to, and b) those who don't need to buy them, but still do. All these carbon credits really represent is a permit to produce some amount of CO2 emissions, because the credits were created and sold by some project that captured and sequestered some amount of CO2 emissions.
Connecting the dots:
It's not clear whether Idemitsu is producing it's own bio-based naphtha, or if it's buying it from someone like Neste, but when you zoom out the situation is the same: we're talking about replacing crude oil with vegetable oil, and we're talking about offsetting transport emissions, not reducing them. Buying a more expensive feedstock and enough carbon credits to negate transport might enable some polystyrene produce to sell an eco-version of their existing product, but is this mass-balance and offset combo really something that can scale? And does that matter, or does it just need to get the ball rolling?
SPONSORED
Wake up with Morning Brew: your daily shot of business news
The Column was born out of inspiration from Morning Brew鈥攖here was plenty of news out there, but finding sensible and brief coverage was a pain. Morning Brew curates the most relevant and important news stories from around the world, and presents them in a fun, engaging, and free newsletter.
Stay up-to-date on the non-chemical business world is a valuable endeavor, and Morning Brew is a great way to get started. Join over 4 million people who start their day with Morning Brew鈥檚 newsletter and discover why they鈥檙e the ultimate source of business news.
SUSTAINABLE CHEMICALS

BASF's bio-based propylene glycol tech
German chemical company, BASF, is providing Poland's largest refiner, PKN Orlen, with their glycerol-to-propylene-glycol process technology at Orlen's biodiesel site.
A little glycerol 101:
Glycerol usually comes up when we talk about biodiesel, because it's a by-product of biodiesel production (we make biodiesel by reacting methanol with vegetable-based triglycerides). There's nothing problematic about molecule itself鈥攜ou can use propane-1,2,3-triol for quite a few applications, it's really just that biodiesel producers would rather produce biodiesel than some byproduct with different economics. (For clarity's sake, we just talked about vegetable-based triglycerides above; note that renewable diesel is not the same thing as biodiesel.)
Okay, so propylene glycol?
Propylene glycol (PG) is typically made via the hydrolysis of propylene oxide, which is made a few different ways, but starts with propylene no matter how you slice it (which ultimately leads back to propane, either from a refinery, or from raw natural gas). Instead of going that route, you could hydrogenate glycerol to make PG, and that's what BASF's process does. The details aren't spelled out, but apparently BASF's process "enables the hydrogenation in [the] liquid phase without any need for separation of intermediates or solvents, leading to lower energy consumption".
What that means:
Until now, Orlen has been exporting the glycerol that plant produces, but they're converting it into PG on-site, so now they can either a) export a premium bio-based product (bio-PG) to a wealthier nation, or b) keep that PG captive and use it for their own economy, perhaps for use as a solvent, surfactant, moisturizer, or airplane de-icer. It sounds like the latter is more appealing: per the press release, they are the "first Polish producer of propylene glycol aiming to meet 75 percent of the country's propylene glycol needs."
Some more headlines
LyondellBasell announced a 5% increase to its quarterly dividend
Maire Tecnimont will design a $1.5B polypropylene plant in Vietnam
Petrofac landed a $1.5B EPC propane dehydrogenation project in Algeria
Novolex's shopping and lawn bags are certified to be compostable
LanzaTech and Plastipak made PET with sustainable ethylene glycol
Molecule of The Day
Today's MOTD deserves a round of applause, it's acrylonitrile.

First synthesized by a French chemist in 1893, the world now produces over 6 million tons of acrylonitrile each year.
Prior to 1960, most of the world's acrylonitrile was made by reacting ethylene oxide or acetylene with hydrogen cyanide. But after DuPont introduced Orlon (an acrylic fiber that is no longer produced) in the 1950s demand for the molecule increased rapidly鈥攁nd a better way to make acrylonitrile arrived. Today, virtually all acrylonitrile is made by the catalytic ammoxidation of propylene.
About a third of the stuff is used to make polyacrylonitrile (which becomes carbon fiber), a third for ABS and SAN resins, and most of the rest to produce acrylamide (which becomes PAM and cleans water).
The main companies making all this acrylonitrile are Ineos, PetroChina, Ascend, and a few more.
The reboiler
Course: We think of chemical plants in terms of unit operations. To understand the industry you need to learn about those units.*
Podcast: Check out this episode featuring a former Global R&D Director at Dow Chemical about sustainability and circular economy.
Safety Moment: Proper documentation for chemicals within the workplace is critical鈥攆amiliarize yourself with these standards for proper hazard identification from OSHA.
The bottoms

Want to discuss this stuff with other readers? Join the Discord.
Interested in working for a startup? Join the talent pool.
Looking for older editions? Read the archive.
Curious about more than just news? Subscribe to Feedstockland.
Reply