- The Column
- Posts
- 🏠Membrane moves
🏠Membrane moves
CMS raised a Series A, Origin Materials’ PEF progress, and toluene.
TOGETHER WITH
Good morning. I was surprised to see CMS leaning into carbon capture since I didn’t know that was a possibility for their membranes—if you’re familiar with their process or the material they are using, please reach out!
From the condenser:
· CMS raised a Series A
· Origin Materials’ PEF progress
· MOTD: toluene

Compact Membrane System’s Series A
Sustainable separations startup, Compact Membrane Systems (CMS), raised a Series A funding round of $16.5 million, led by Pangaea Ventures, and including GC Ventures, Solvay Ventures, Chevron Technology Ventures, and Technip Energies.
Getting you up to speed:
We’ve talked about CMS once in the past—their silver-embedded amorphous fluoropolymer membrane has shown promising results in olefin-paraffin separations, so they’re trying to deploy it at polypropylene (PP) plants in propylene recovery. But the technology seems to have broader applications—over the last 6 months, CMS has signed a few agreements to pilot its membranes for CO2 capture from flue gas: first with Braskem (who was their primary partner for propylene recovery), then with RHI Magnesita, and most recently with Voestalpine.
Okay, so they raised some money?
Now that they’ve successfully demonstrated these membranes for propylene recovery, and have agreements in place for a (much) larger market (point source CO2 capture), CMS is shifting into execution mode: the “Series A funding will accelerate the development and commercialization of their olefins and carbon capture solutions, with the goal of delivering a low-cost, fully electrified solution by 2026”.
Zooming out:
CMS hasn’t disclosed what fraction of the CO2 in the flue gas they’re able to capture, but it might be mute point: even if it’s a small fraction, they’re still able to do it in a modular fashion with electricity alone (membrane-based separations are pressure driven, not heat driven, and they don’t use any chemical solvents to do the separation). That immediate benefit, even if marginal, should drive adoption from hard-to-abate sectors like steel and cement who need easy-to-achieve near term emission reductions.
SPONSORED
Looking for training on CCUS?
You’ve probably noticed that the discussion around capturing CO2 has been heating up lately—but it’s not all talk—companies are actively constructing Carbon Capture Usage and Storage (CCUS) projects in many parts of the world, and proposing many more. But just how feasible is this technology? Can it stand up against alternative, carbon-neutral technologies?
ESD Simulation has been working on these projects for many years, and is stepping in to dispel the confusion and put practical solutions first. Their course on CCUS breaks it down into three stages: actually capturing the CO2, getting the CO2 where it needs to go, and putting that CO2 to use.
Head over here to learn more, and be sure to use The Column’s discount code (THECOL2023) when booking!
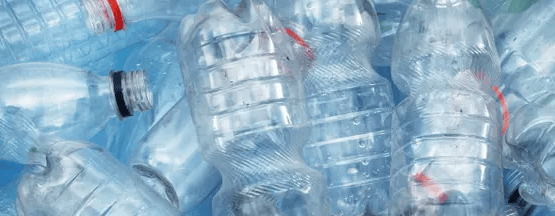
Origin Materials’ recent PEF progress
Sustainable chemicals and materials company, Origin Materials, signed two separate agreements last week to commercialize a couple of furandicarboxylic acid (FDCA) derivatives.
Setting the scene:
Origin’s core process technology converts lignocellulosic biomass into a few different molecules, but chloromethyl furfural (CMF) seems to be the star of the show. That’s because it can be used to make paraxylene, which is what we oxidize to make terephthalic acid (PTA), which is typically esterified with ethylene glycol (MEG) prior to polycondensation into polyethylene terephthalate (PET). But CMF can also be used to make FDCA, and FDCA can also be esterified with MEG—the following polycondensation just makes polyethylene furanoate (PEF) instead.
Okay, so they signed agreements?
The first agreement was with Husky Technologies (a bottle blower), who successfully made bottles using a PET/F hybrid polymer that Origin produced (presumably by blending FDCA with PTA mid-esterification), and the second agreement was with Terphane, who is interested in using PEF to make some biaxially oriented films (BoPET is just PET, but with a unique and mechanically-produced molecular orientation).
Bigger picture:
Being the only producer of carbon negative PET is certainly attractive, but it’s even more attractive if that PET can actually be a little bit PEF, and that PET/F blend offers performance benefits on top of carbon negativity. It’s easy to imagine Origin offering a suite of PET/F blends in the near term (with drop in compatibility) as Origin’s buyers and downstream markets warm up to PEF.
Some more headlines
SK Capital just closed their Catalyst Fund II at $800 million
Technip Energies and Enerkem are working together on waste-to-biofuels
Lanxess' CEO thinks that the German government should do more to help industry
Montana Renewables got it SAF certified via the ISCC
Toray developed a hydrogen-oxidizing bacteria with a fast CO2 fixation rate
Molecule of The Day
Today's MOTD is the one you've been waiting for… toluene.

Owing its name to the balsam of Tolu, the world now produces some 33 million tons of toluene each year.
Most of that toluene is made at refineries thanks to the catalytic reforming of naphtha, but a good bit is made from the production of coke (which you'll see the most of in China). At refineries that toluene is found as a component in BTX and most of it is never separated from its aromatic friends—it's just blended into gasoline.
Even when that toluene is isolated, most of it ends up being used to make B and X (benzene and xylene). The rest is used to make TDI (for polyurethanes), TNT (for blowing up stuff), benzoic acid, and benzaldehyde.
Given that most of the molecule is made at refineries it shouldn't be a surprise that ExxonMobil, Sinopec, and Shell are some of the key players.
The reboiler
Podcast: Check out this episode on education, talent development, and diversity in the chemical industry.
Article: North Carolina’s old lithium mines are being revived by vehicle electrification.
The bottoms

Want to discuss this stuff with other readers? Join the Discord.
Interested in working for a startup? Join the talent pool.
Looking for older editions? Read the archive.
Curious about more than just news? Subscribe to Feedstockland.
Reply