- The Column
- Posts
- 馃彮 Ethanol from natural gas
馃彮 Ethanol from natural gas
Iran's methanol-to-ethanol plans and more VAM is coming to India
Good morning and Happy New Year! Hopefully everyone had a slower past couple of weeks and didn't miss chemical news all too much. If you're new here (up to 8,770 of you now!) the newsletter is typically sent on Mondays for free subscribers, and also on Wednesdays and Fridays for paid readers.
From the condenser:
路 Iran's methanol-to-ethanol plans
路 More VAM is coming to India
路 MOTD: acetic acid

painting of chemical plant in persia
Iran wants to make ethanol from natural gas
Iranian chemical company, Zagros Petrochemical, has selected China's Dalian Petrochemical's methanol-to-ethanol process technology for a new plant in Iran.
A little ethanol 101:
Today, virtually all of the ethanol we produce today is made by fermenting glucose. Usually that glucose comes from starch, but it can also come from cellulose (which we've talked about recently). Either way, that ethanol ends up being used as a gasoline oxygenate (mostly), as a solvent or disinfectant (sometimes), or as a feedstock to make ethyl acrylate, ethyl acetate, and ethylamines (rarely).
So, what's the deal here?
For various reasons鈥攕uch as anti-alcohol laws, a semi-arid climate, and salty soil鈥擨ran has historically imported all of its ethanol. That was already set to change in a few months when the country's first fermentation-based site starts up, but now, with this new methanol-to-ethanol site on the horizon, Iran will no longer need to import any ethanol (the upcoming methanol-to-ethanol site is 5x larger than the fermentation-based site).
Zooming out:
Producing ethanol from methanol means converting natural gas (which Iran has a lot of) into syngas, converting syngas to methanol, and then reacting that methanol with carbon monoxide. That last step isn't normal, but that doesn't mean it can't make sense鈥攇oing the petrochemical route means: (1) reduced need to import/cultivate starchy feedstocks, (2) higher yields and scaling efficiencies that can't be achieved via fermentation, and (3) greater local valorization of domestically produced natural gas.

painting of buckets that have steam
Some more VAM is coming to India
Indian paint company, Asian Paints, has selected KBR and Showa Denko's vinyl acetate (VAM) joint process technology for a new site in India.
The context you need:
The world produces roughly 8 million tons of VAM each year, almost exclusively by the reaction of ethylene, acetic acid (usually referred to as GAA), and oxygen. Usually that VAM is then polymerized to make polyvinyl acetate (some of which is then hydrolyzed to make polyvinyl alcohol), but it's sometimes used to make polyvinyl butyral or co-polymers with some more ethylene. In any case, pretty much all of these molecules and their derivatives end up in things like coatings, paints, and adhesives.
What's going on here?
While VAM is commonly polymerized to make polyvinyl acetate (as mentioned above), Asian Paints wants to polymerize it with more ethylene to make a vinyl acetate ethylene (VAE, not to be confused with EVA) emulsion. And in case it wasn't obvious, Asian Paints wants to use that VAE emulsion to make paints.
Bigger picture:
Since the construction of new VAM plants typically coincides with middle class expansion in developing countries, it's easy to write off this announcement as another case of application expansion. But this situation is unique鈥擵AE emulsions are known for their use in low-VOC paint formulations鈥攕o application replacement is the true growth mechanism here (where less environmentally friendly paints are being replaced with more environmentally friendly paints).
Some more headlines
C&EN covered Alterra's pyrolysis plant in Akron, Ohio
PKN Orlen completed its acquisition of an LDPE unit in Poland
Brenntag decided to stop talking to Univar about merging
Indorama Ventures had a fire at its PTA plant in Spain
BP's acquisition of Archaea Energy went through for $4.1B
Product of The Day
Today's MOTD is the most interesting one of all:acetic acid.
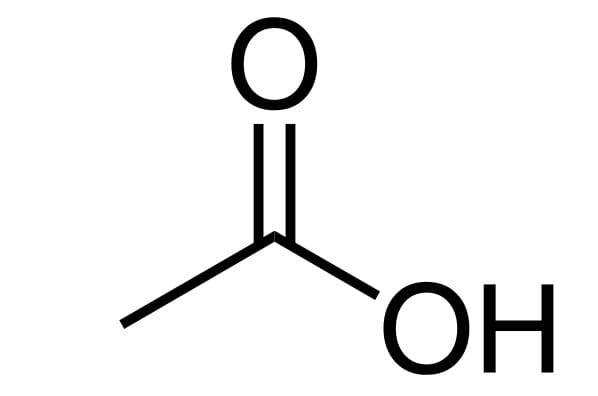
You're probably familiar with acetic acid in its diluted form (vinegar), but only a small fraction (less than 10%) of the 22 million tons of acetic acid produced each year actually end up dressing salads and pickling vegetables.
Most acetic acid (roughly 75%) is produced by reacting methanol with carbon monoxide, but it can also by made by oxidizing acetaldehyde or ethylene. Some of the largest producers of acetic acid are Celanese, INEOS, Eastman, and LyondellBasell.
About 30% of acetic acid is used to produce vinyl acetate monomer, 30% to produce acetic anhydride, 20% to produce esters (like ethyl acetate, n-butyl acetate, isobutyl acetate, and propyl acetate), and 20% to produce terephthalic acid.
The reboiler
Safety Moment: Leverage this flowchart to help with logically identifying chemical reactivity hazards.
Guide: If you鈥檝e been looking for a breakdown of biobased fuels, then look no further.
Learn: The Column gets its name from the separation unit processes. Check out this course to learn why mass transfer operations are the core of the industry.*
Course: Want a complete overview of the major petrochemicals and how we make them? This will cover all the bases.*
The bottoms

Was this email forwarded to you?
Reply